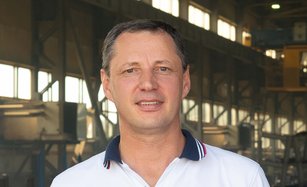
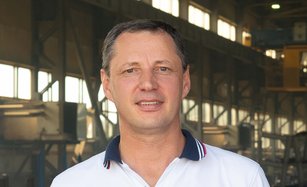
Об итогах участия в нацпроекте «Производительность труда» рассказали на заводе ЖБИ ООО «Спецзастройщик «КСМ»
Компания «Кировспецмонтаж» отмечает в этом году свой 30-летний юбилей. Одно из приоритетных направлений развития КСМ — создание целых микрорайонов с развитой инфраструктурой, объектами торгового, сервисного и спортивно-развлекательного назначения. За время работы компания ввела в эксплуатацию более 1 млн м2 жилья, построила километры пешеходных зон, возвела несколько детских садов.
Ни одно стороннее производство не смогло бы выдержать сроки, качество и объёмы стройматериалов, необходимых компании «Кировспецмонтаж», поэтому в 2006 году было принято решение о создании собственного высокотехнологичного производства. Так появилась производственная база, на которой трудятся около 1000 специалистов высокого класса.
Сегодня на 16 гектарах земли находятся цеха по производству стеновых панелей для панельного домостроения, по производству сборного железобетона, производству изделий для мощения и благоустройства территории, производству светопрозрачных конструкций. Также есть собственная автотранспортная база (более 100 единиц) с ремонтными мастерскими и тёплыми стоянками.
В марте 2022 завод ЖБИ ООО «Спецзастройщик «КСМ» вступил в нацпроект «Производительность труда». Инструменты бережливого производства сотрудники предприятия внедряли вместе со специалистами Регионального центра компетенций. В течение полугода рабочая группа с экспертами РЦК выявляли проблематику, работали над устранением потерь, создали эталонный участок, а также подготовили внутренних тренеров, которые в дальнейшем будут тиражировать полученный опыт самостоятельно. А эксперты РЦК будут сопровождать предприятие ещё 2,5 года, оставаясь на связи, проводя консультации дистанционно и выезжая на производство по запросу.
Александр Перфилов, директор производственной базы ООО «Спецзастройщика «КСМ»:
— Если мы не учимся и не развиваемся, то мы отстаём от времени. Существующая экономическая ситуация заставляет искать резервы для удержания стоимости продукци. Наша компания остаётся социально ориентированной: белая зарплата сотрудников, оплачиваемые отпуска и больничные. Мы обеспечиваем работников спецодеждой, бесплатными обедами в собственной столовой, у нас есть развозка сотрудников по городу на завод и с него. Компания постоянно вкладывается в производство, мы ежегодно обновляем оборудование, поддерживаем в надлежащем состоянии корпуса производственной базы и ее территорию. В своё время мы закупили европейские линии по производству железобетона. И это линии с технологией, а не просто станки. Всё это — затраты предприятия, которые влияют на себестоимость продукции. Мы не можем экономить на входящем сырье, так как по данной технологии оно должно быть качественным. Компания дорожит своими сотрудниками и идет по пути сохранения штата и поддержания рыночной заработной платы. Многие сотрудники работают со дня основания компании и вносят свой вклад в ее развитие. Остаётся снижать себестоимость продукции за счет других инструментов. Поэтому когда мы узнали о нацпроекте «Производительность труда», решили принять в нём участие. Результаты уже есть: не вкладывая огромных финансовых средств, мы начинаем снижать себестоимость продукции. Это происходит за счёт перераспределения нагрузки, облегчения работы сотрудников, выявления скрытых резервов, уменьшения брака и отходов.
Подчеркну, мы всегда стремились к бережливому производству. Делали это постоянно, но по наитию, без научного подхода. Сегодня специалисты РЦК дали нам для этого проверенные, работающие инструменты, которые мы сейчас применяем.
Видимый результат внедрения инструментов бережливого производства — время протекания процессов сократилось на 18%. Например, времени на производство железобетонной колонны теперь требуется на 15 часов меньше.
Виктория Кушова, инженер по развитию производственной системы завода ЖБИ:
— Достигнуть таких показателей нам удалось за счёт того, что мы стали меньше времени хранить изделия в цехе. Они вывозятся на склад готовой продукции, и у нас освобождается место в цехе для нового производства. Также у нас повысилась эргономика производственных цехов. На эталонном участке — в арматурном цехе применены 4 шага системы 5С.
Николай Зубарев, инженер по развитию производственной системы завода ЖБИ:
— Система 5С реально работает. Внедряя её, мы разложили всё по местам согласно технологических карт, постоянно поддерживаем порядок, соблюдаем чистоту, сортируем и стандартизируем. Стандартизация — это прописывание определённых стандартов для каждого рабочего места: как протекает операция на данном рабочем месте, как здесь должен храниться инструмент и т.д. Каждый сотрудник знает эти стандарты и придерживается их во время работы.
Виктория Кушова , инженер по развитию производственной системы завода ЖБИ:
— Кроме того, мы создали матрицу компетенций. В ней прописано, какими компетенциями обладает тот или иной сотрудник, на какие участки его можно поставить, чему важно обучить, чтобы повысить его компетенции. Благодаря этому, когда руководитель цеха отпускает кого-то в отпуск или на больничный, он знает, кем его заменить. Процесс не останавливаются, и замена никак не сказывается ни на времени протекания, ни на качестве. Также это помогает принимать кадровые решения (продвижение по карьерной лестнице).
По словам сотрудников производственной базы, огромное понимание действия инструментов бережливого производства дала деловая игра на Фабрике процессов Регионального центра компетенций. В созданных на Фабрике реальных условиях производства можно на практике увидеть, как улучшения влияют на операционные и экономические показатели.
Николай Зубарев, инженер по развитию производственной системы завода ЖБИ:
— На эталонном участке мы разработали систему подачи арматуры в рубочный станок, чтобы рабочий тратил меньше времени на забор арматуры. Также у нас разработана система приёма арматуры с рабочего станка. Всё автоматизировано собственными силами, меньше движений, выше скорость производства. Также мы разработали 2 вида тележек для сварщиков. Теперь сварочные аппараты у нас мобильные. Подобные тележки мы увидели именно на Фабрике процессов и решили внедрить у себя. В ближайшее время Николай и Виктория поедут в Москву в Школу тренеров, после чего смогут обучать применению инструментов бережливого производство других сотрудников предприятия.
Александр Перфилов, директор производственной базы ООО «Спецзастройщика «КСМ»:
— Вместе с РЦК мы запустили на предприятии безостановочный процесс повышения производительности труда. За 3 года участия в программе мы должны достигнуть повышения целевых показателей производительности труда на 15%. И я уверен, мы с этим справимся!
Стать участником нацпроекта может предприятие, имеющее выручку более 400 млн. рублей, а также осуществляющее свою деятельность в следующих отраслях экономики: обрабатывающее производство, сельское хозяйство, транспорт, торговля и строительство.